160TPD Wheat Mill Machinery technology introduction:
1. cleaning part
2. milling part
3. packing part
1. Cleaning part
To clean out the middle and small impurity from wheat. e.g., dust, stone, magnetic material, wheat was bitten by insect and so on. Includes beating, screening, destoner, magnetic separator and dampening. This section is to prepare for milling part and to protect the machinery as well.
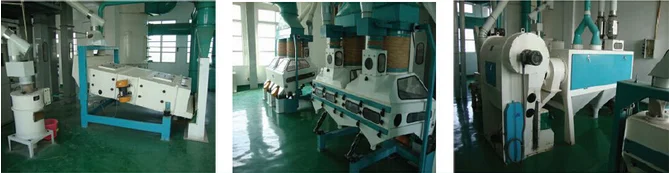
2. Milling part
The second step, to mill the grain and separate the flour, bran and other by-product:
(1) Mill: mill the grain to break the integrity by the roller moving.
(2) Sifter: to separate the flour,bran and other by-product, also separate large size and small size to ensure flour quality.

3. Packing part
The third step, the packing machine can be manual or automatic weighting and packing.

4. PLC controlling system
To controlling the whole set of machinery to work well and showing the process of working.
Scheme requirement:
1. Technical process introduction
1.1 The following 160TPD wheat mill machinery is specially designed according to hard wheat.
1.2 This design adopts the technical process of extracting flour from medium and long flour scheme in the milling workshop and 10 MMD25/100 pneumatic automatic roller mills to consist the 4B7M1S1T milling technique with 4 purifying and two bran scourings which is full blown in Europe. 4B has coarse and fine systems; bran pieces from upper section of plansifter is treated with bran scourer to shorten the process of break system. Middling system, semolina system and 1T system all adopt smooth rollers and combine with impact detacher to reduce the power of rear milling stage. Roller’s contact length is 12.50mm/100Kg wheat•24h; sieving area is 0.088m2/100Kg wheat•24h; purifier’s unit sieve surface width is 1.84mm/100Kg wheat•24h.
1.3 In consideration of environment protection requirements, it’s suggested that dry cleaning method which is usually adopted by Europe be used for wheat cleaning process and meanwhile intensive dampener with computer feedback device be used to reach the moisture suitable for milling. The process includes two sievings, two scourings, one de-stoning, two dampenings, three magnetic separatings and multiple air suctions before the clean wheat enters break system. This is to ensure wheat purity. All the equipment is fully enclosed.
1.4 In tropical humid areas, 18 hours conditioning time is required for clean wheat before it enters break system; in tropical arid areas, the conditioning time is longer than 18 hours.
1.5 This technical process has the following economic and technical index: if it mills one grade, total flour extraction rate is 75%, cumulative ash content is 0.53~0.62%; if it mills two grades, the extraction rate of grade 1 is 45%, its ash content is 0.45~0.55; the extraction rate of grade 2 is 30% and its ash content is 0.65~0.73%. The above mentioned ash content is calculated on dry basis. For normal milling, the power consumption per ton flour is not higher than 65kW•h.
1.6 Flour is transported to packing workshop 120 meters away by conveying system. There is a small bag packing workshop 20 meters away from milling workshop. A electric valve distributes the flour to either packing workshop.
1.7 Inferior and bran are packed directly. All the organic leftovers will be crushed by a crusher and then mixed with bran.
1.8 Total installed capacity is 640kW.
1.9 Flour conveying system is equipped with an entoleter. Its principle is to destroy the worm eggs hidden in the flour by the machine’s high speed rotation. With this entoleter, flour storage time is improved by 3~5 times.
2. Preparation work by the client
Client should provide the drawings of terrain and landform so that we can adjust and design the workshops in time.
3. Requirements for raw wheat
We will design the production processes according to raw wheat and requirement for flour, so client should provide the wheat sample or samples (of each type and the proportions). We will analyze the samples in the lab in order to design rational technique. It’s suggested that client should at least 1.5Kg of each type of the wheat used for milling.
4. Capacities of finished product & by-product and by-product treatment:
4.1 The first production week after installation is the breaking in period and the capacity is 140T/24h;
The tested capacity can reach 180T/24h in the second production week after installation;
The normal capacity is 160T/24h.
4.2 For product yield, please refer to 1.5; product treatment in 1.6.
II. Wheat mill machinery part
1. Client is responsible for civil engineering and foundation and needs to prepare water, 3-phase electricity, crane and forklift for loading and unloading equipment, welding machine, cutting machine, 8-10 installation workers with fluent English ability. We will provide 1 installation engineer and 3 technicians. We’ll also provide necessary installation tools and materials.
2. The quotation of the wheat mill machinery includes the complete set of main equipment, auxiliary equipment, cables/wires and pipeline, etc; but we only supply the cables between the secondary switchboard and equipment, not the cables between the secondary switchboard and primary switchboard & transformer.
3. Control system: PLC and electric cabinet bilateral control to realize the following functions:
a. Automatic display of the instantaneous flow rates of raw wheat, clean wheat, flour, inferior flour and bran;
b. Automatic display of the percentages of raw wheat, clean wheat, flour, inferior flour and bran;
c. Automatic display of the flow rates of raw wheat, clean wheat, flour, inferior flour and bran in a specified period;
d. Check historical flow rates;
e. Malfunction alarm system;
f. Printing function.
III. Others
1. Daily water consumption is 8 ton;
2. Labor force: 8 hour work shift; 1 worker for control room, 1 worker for milling section, 1 worker for cleaning section; 2 workers for packing; other workers for raw wheat and flour conveying are nott included.